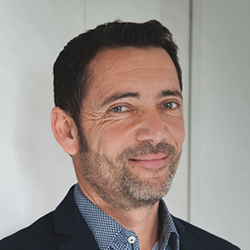
Philippe Dubernet
Philippe Dubernet started working for the Air Health and Safety field as Unit Manager at the APAVE Bordeaux Agency in 2007. He joined the Operational Division of APAVE SUDEUROPE in 2018, where he now holds the position of Technical Support Development Manager within Testing & Measurements.
Improve your teams’ working conditions
thanks to indoor air quality
Hello Philippe. With the current pandemic, we are talking again about indoor air safety but this subject is not new to you, besides Covid-19?
Indoor air quality is quite simply a major health issue in France. A study by Santé Publique France - carried out in 2016, i.e. well before the pandemic - estimates that there are 48,000 premature deaths each year in France due to air pollution. This is therefore the second most preventable cause of death, after smoking and before alcohol. We should also remember that indoor air is 5 to 7 times more polluted than outdoor air and that we spend 80% of our time in enclosed spaces, at home, at work, while travelling, etc. We have been concerned about these issues in our country since the 1970s through health regulations and they have been strengthened to include the regulatory system for monitoring air quality in buildings open to the public. More widely used, the quality of workplace atmospheres is governed by the provisions of Articles R4211-1 and following of the French Labour Code, which distinguish two responsibilities: that of the contracting client for the design of the workplaces and that of the employer for the use of these places. The latter must ensure its employees breathe clean air. Two fundamental obligations for employers are to maintain a minimum air volume and guarantee an air renewal threshold. Without going into details, however, several types of premises must be distinguished: those with non-specific pollution, i.e. premises where air pollution is due only to a human presence, sanitary premises and premises with specific pollution in which air can be polluted by substances that are troublesome or dangerous to health (gas, steam, solid or liquid aerosols). Depending on the situation, the rules are of course different.
Public organisations, particularly schools, have been made aware of these issues since the application of the regulatory obligations published in 2015 and the numerous communications associated with IAQ, as well as for companies in the chemical or industrial sectors that have specific obligations.
With the pandemic, there are now new ministerial recommendations on air quality aimed in particular at strengthening renewal and limiting recycling of air. These specific recommendations are also applied sector by sector and are then accompanied by other recommendations (information, behaviour, etc.). But even though the current situation news has heightened awareness about the importance of air quality in organisations, the problem remains under-estimated by a large number of companies. In fact, controlling the factors relating to the quality of the working environment and therefore health means participating in the well-being and performance of people in the workplace. However, it is not only a health issue but also an economic one. In France, poor indoor air quality is estimated to cost €19 billion per year.
Before measuring the possible presence of a pollutant, you systematically start your checks by assessing the means of ventilation, why?
This is absolutely fundamental, regardless of the pollutants in an enclosed space (benzene, formaldehyde, carbon monoxide, particles, viruses, bacteria, yeasts, moulds, etc.). If ventilation is of poor quality, there will be a cumulative effect that can be particularly harmful in the short, medium or long term. For some companies that do not have any ventilation systems other than windows, cold periods are necessarily complicated. Paradoxically, however, the most problematic situations that can be met are often connected to buildings whose ventilation is exclusively mechanical. Indeed, ventilation systems that are not maintained and whose performance is unknown may contribute to the deterioration in air quality, or even become the source of a health risk. In these cases, it is often the emergence of symptoms such as headaches, fatigue, irritation of the eyes, nose, throat and skin, dizziness as well as allergic reactions and asthma that alert the company manager. These pathologies can develop silently. People may only take sick leave after a certain time and it is insidious. An assessment of the ventilation means and the creation of monitoring files or even a health record make it possible to prevent these risks and meet the regulatory requirements that are too often poorly understood.
What are the solutions for companies? What does an inspection entail?
The first thing is ensure the ventilation equipment is properly maintained. It is also necessary to check that it is suitable for the working environment and/or properly sized. A typical case is an enlargement of the company, a modification of the premises without adapting or resizing the ventilation system or a failure to take into account the ventilation and sanitation aspect on taking delivery of the building.
From a technical point of view, when monitoring air quality in addition to assessing the ventilation means, there may be associated regulatory controls of a series of pollutants known as “interest pollutants”:
- formaldehyde, an irritant for the nose and respiratory tract, emitted by certain building materials, furniture, certain adhesives, maintenance products,
- benzene, a carcinogenic substance resulting from combustion (exhaust gases in particular),
- carbon dioxide (CO2), representative of the level of confinement, a sign of an accumulation of pollutants on the premises,
- radon, classified by the International Agency for Research on Cancer as a definite carcinogen for the lungs since 1987.
These checks are carried out under COFRAC accreditation.
Where symptoms, smells, etc. have arisen that may be connected to air quality, our current checks combine an assessment made by our employees who combine an inspection of the condition of the ventilation and sanitation of the work premises with monitoring of the chemical and physical parameters linked to air quality. This monitoring involves new technologies (sensor systems) that are placed in strategic locations on the sites to be monitored, allowing precious information to be tracked over a longer period of time to identify the presence of pollutants according to the company's activities. These devices collect data that allow us to improve our diagnoses and also to have a continuously updated overall understanding of the most active pollutants in the working environments.
Besides the technical part, there is now a strong need for advice and training, particularly for new property programmes where air quality is becoming a major environmental issue. We provide assistance to building managers and site managers with implementing policies for managing and controlling air quality through training as IAQ reference persons and with preparing a health record, an essential tool for monitoring the health quality of a working environment.
On the same
topic